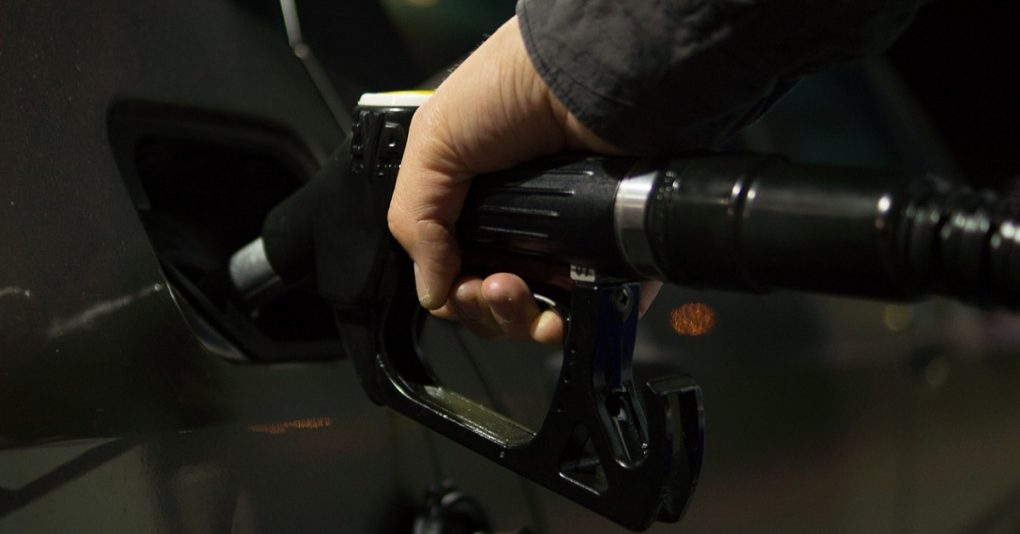
Making ethanol gas at home is very possible and very easy. Ethanol is used to fuel vehicles, power tools, and pretty much anything with a gas powered motor. Making your own ethanol can save you a lot of money on your regular fuel bill, and it’s very easy to do, so why not?
The first, and most important step to producing your own ethanol is getting a permit to do so. You must acquire a Fuel Plant Permit from the Bureau of Alcohol, Tobacco and Firearms to produce any amount of ethanol legally. Now, before you put your homemade ethanol gas into any motors, check what your gas tank and other fuel system components are made out of. Ethanol is extremely corrosive and can be damaging to aluminum and plastic. Be sure to read the user’s manual and follow the manufacturers guidelines to ensure that your fuel will power your gas engine, not destroy it.
To start, you will need these ingredients:
- Sugar – 40lbs.
- Brewer or distiller yeast – 10oz.
- 20 gallon barrel (with a lid) – 1
- Large stirring paddle – 1
- A still
Step 1
First, identify an out-of-the-way spot that maintains a consistent temperature of 70°F. You’ll place your full barrel here once you’re finished.
Next, heat 10 gallons of water to about 100°F and then transfer it into your 20 gallon barrel. Mix your sugar into the water- about 10 pounds at a time- for easy mixing. Once the sugar is mostly dissolved, you can fill the barrel most of the way with more hot water. Keep close track of the water temperature. When the sugar water reaches 80°F-90°F, you can add in your yeast and stir it thoroughly. Secure the lid loosely (oxygen is necessary for this process) on the barrel, transfer the barrel to the identified spot, and leave it to begin fermenting
Step 2
The fermentation process will start quickly- bubbles forming at the top of the solution will let you know that it’s working. Remember to keep the barrel lid on loosely. Fermentation should have taken place within about a week. When bubbles stop forming at the top of the barrel, the process is complete.
Step 3
After the fermentation process is finished, you will need to filter it. Straining your ethanol will filter out any bugs that may have gotten inside, and also dead yeast.
Step 4
The filtering process will leave you with a solution of water, dead yeast, and ethanol. You will need to use a special still to separate the ethanol from the other substances. This is the distilling part of the process, and it will leave you with about one third of the amount of solution you began with.
Step 5
Lastly, you have to ‘dehydrate’ the ethanol to remove any remaining water. Specific filters are required for this part; these filters retain water molecules while allowing ethanol molecules to pass through.
When you’re completely finished, about a quarter of your original solution will be pure ethanol. Now to make this ethanol usable for most gas engines (and to reduce the risk of corrosion), you will have to mix it with gasoline. About 15% gasoline to 85% ethanol is the ideal mixture.